5 Misconceptions About Custom Metal Fabrication Companies
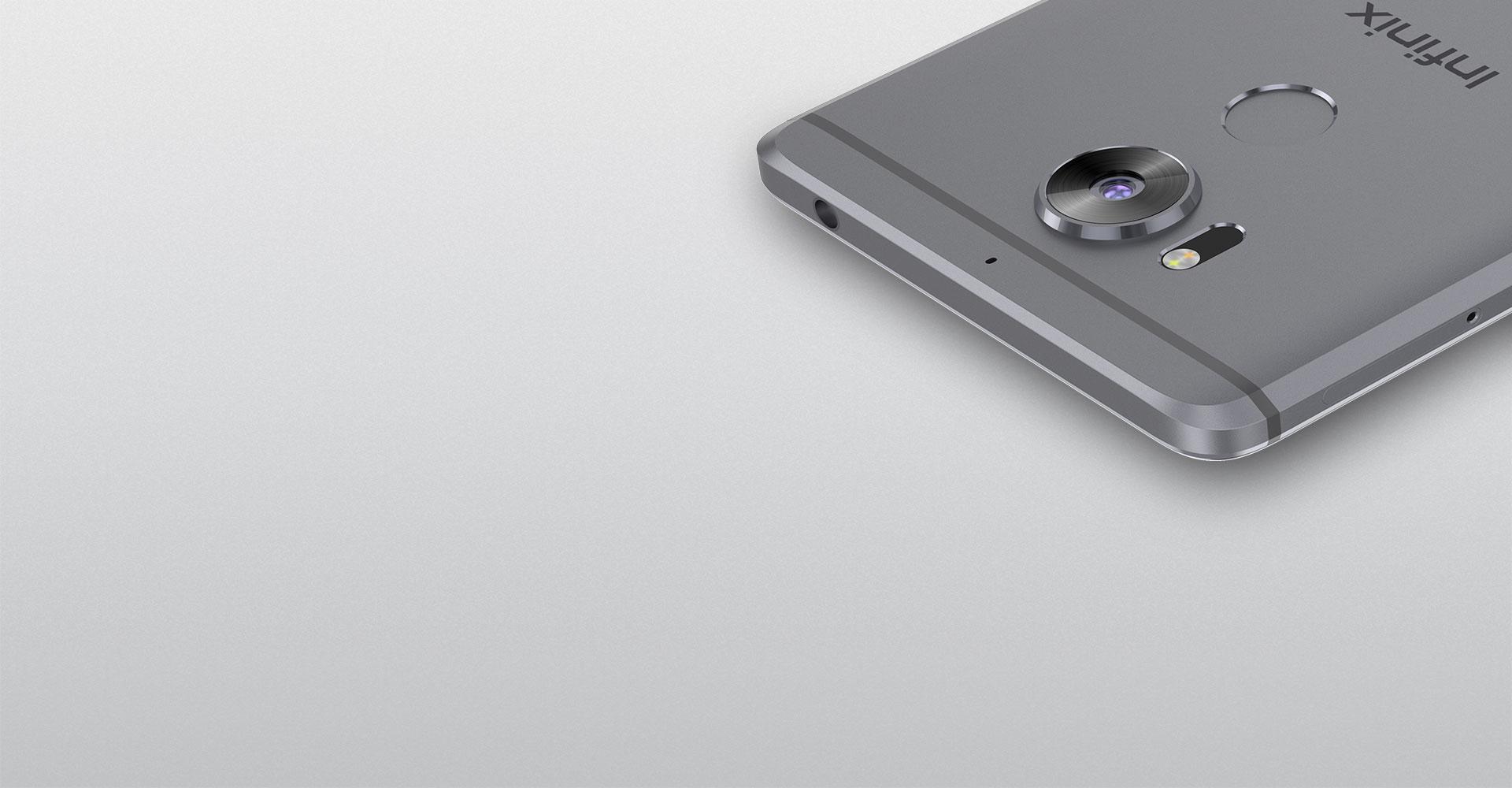
Suppose you are looking for a custom metal fabrication company to work on your fabrication project. In that case, you may easily find yourself overwhelmed even when searching for answers to even the most basic of questions.
Metal fabrication is a term that’s already confusing enough since it broadly refers to the numerous processes involved in cutting, shaping, welding, machining, or moulding metal material into the desired final product.
A full-service custom metal fabrication company isn’t just a business but rather an internal grouping of technologies applied at different stages of production for the fabrication of the desired end product.
When researching a fabrication company, it is important not to be sidetracked by generalizations and misconceptions about what a custom metal fabrication company can and can’t do. Your goal should always be to know what to expect from a fabrication company.
Here are five common misconceptions that you need to know about when doing your research to help you choose the best company possible for the project:
- All Metal Fabrication Companies Are the Same
Metal fabrication companies may offer just one service to their customers or just one service. The reality is that services offered vary widely from one shop to the next. Selecting one over the other directly relates to the requirements of the project. You need to find a fabrication company that offers the services required to complete the project to your level of satisfaction.
The first step should be to evaluate the capabilities of the metal fabrication company. The shop should be capable of performing the fabrication method needed to complete your specific part’s geometry and be familiar with the materials used in its fabrication.
Related to this, you need to ensure that the fabrication company serves your industry and meets the space requirements for your project. The building needs to be sufficiently large to fulfill the needs of your project without impeding or slowing down production. Find a full-service metal fabrication shop that satisfies all your project needs.
- You Don’t Need an Engineer If You Have a Design
A common misconception is that you don’t need further input from an engineer if you submit your own design. However, the reality is that from concept to the actual manufacturing of a product is a process involving multiple steps that require engineering input throughout.
Even after you submit the final design for your project, you still require the expertise of an engineer for tweaking, testing, and prototyping. Fabricators and engineers work together throughout all processes to ensure that end products work as designed.
- The Best Price Will Ensure a Better ROI on Your Project
The old saying that if you find the best price for the best quality, you are likely to get the most value for your money has some truth in it.
Preparing a budget when researching your new fabrication project is critical to ensuring the project’s financial success. However, you should always remember that, in the long run, the lowest price from a fabricator isn’t necessarily guaranteed to provide a better ROI.
Fabricators generally adhere to 2 types of business models when competing for your business. While some compete purely on price, others compete on the overall value of their work. The distinction here is cost vs. quality. Finding a balance will be to your advantage, but you need to invest in value to ensure a better ROI on your project.
- Metal Applications Are Interchangeable
While you have many metals to choose from when designing your metal fabrication project, some that have similar characteristics, it doesn’t automatically mean that you are free to use the metals interchangeably to complete your project.
The material composition of metals varies. Each metal has its own set of unique properties with specific characteristics for specific applications and end products.
One excellent example is a common misconception that you can substitute steel for aluminum and vice-versa in fabrication projects. Aluminum is more ductile, softer, and considerably lighter than steel. It is commonly used to fabricate components and parts in the transportation sector or for assorted packaging. However, it lacks the strength of steel and is more expensive too. If you are looking for resilience and durability, you should definitely avoid substituting steel for aluminum in your fabrication projects.
- Custom Metal Fabrication Companies Use Multiple Vendors
While it is definitely possible to bring in a third-party vendor on a new project in some shops, you will hardly ever find a full-service fabrication company using the services of one or multiple vendors to complete a new project.
No matter how unique the project might be, from start to finish, design, fabrication, assembly, and engineering are all done in-house. When you research a metal fabrication company for your new project, you should look for a company that’s capable of fabricating from multiple metals, such as carbon steel, stainless steel, brass, copper, and aluminum, that uses state-of-the-art equipment operated by skilled craftsmen all done under one roof.